Amazing Info About What Are Types Of Branch Connections
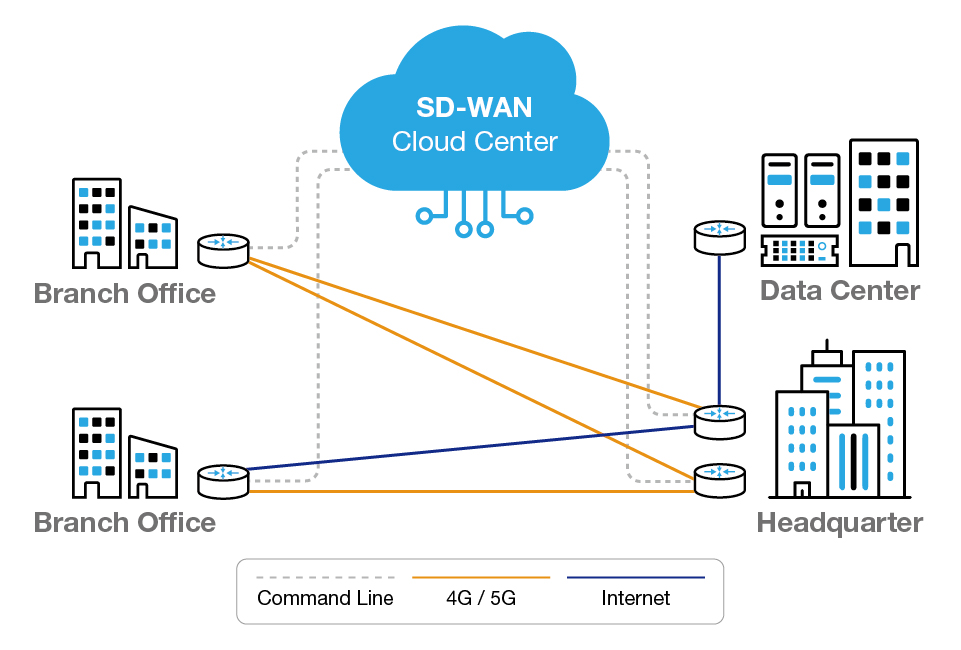
Understanding Branch Connections
1. Why Branch Connections Matter
Ever wondered how those pipes magically split off in your home's plumbing, or how complex networks of pipelines distribute resources across vast distances? The answer, my friends, lies in the ingenious world of branch connections. These aren't just simple splits; they're carefully engineered junctions that ensure the smooth and efficient flow of fluids or gases. Think of them as the circulatory system of your infrastructure, vital for keeping things running. Without them, you'd have one long, boring, and ultimately useless pipe!
Branch connections are everywhere, from the intricate plumbing in your bathroom to the massive pipeline networks that crisscross the country. They're the unsung heroes of infrastructure, working tirelessly behind the scenes to keep our lives comfortable and convenient. So, the next time you take a hot shower or fill up your gas tank, take a moment to appreciate the humble branch connection.
But what exactly are branch connections? Simply put, they're the methods used to join a smaller pipe (the branch) to a larger pipe (the main line or header). The way this connection is made significantly impacts the strength, reliability, and flow characteristics of the entire system. Choosing the right type of branch connection is crucial for ensuring safety, efficiency, and longevity.
So, let's dive into the fascinating world of branch connections and explore the various types available. Prepare to be amazed by the ingenuity and engineering prowess that goes into these seemingly simple junctions. Trust me, it's more exciting than it sounds! Okay, maybe not that exciting, but definitely more interesting than watching paint dry.

Branch Connections Detail .dwg Thousands Of Free CAD Blocks
Common Types of Branch Connections
2. Welded Outlets
Welded outlets, such as weldolets, sockolets, and threadolets, are among the strongest and most reliable types of branch connections. As the name suggests, they are welded directly onto the main pipe, creating a permanent and leak-proof seal. This makes them ideal for high-pressure and high-temperature applications where safety is paramount. Think of them as the bodybuilders of branch connections: tough, dependable, and ready to handle anything you throw at them.
Weldolets are generally used for butt-welded connections, offering a smooth transition and minimal flow restriction. Sockolets, on the other hand, are used for socket-welded connections, providing a strong and reliable joint that's relatively easy to install. Threadolets are used for threaded connections, offering a convenient and cost-effective option for low-pressure applications.
The choice between these three depends on the specific requirements of the application. Weldolets offer the best strength and flow characteristics, while sockolets provide a balance of strength and ease of installation. Threadolets are best suited for situations where quick and easy connections are needed, but strength is not a primary concern.
One thing to keep in mind is that welding requires skilled technicians and specialized equipment. It's not something you can just do in your garage with a DIY kit. However, the long-term benefits of a properly welded connection far outweigh the initial investment.
3. Threaded Connections
Threaded connections are a popular choice for low-pressure applications where speed and ease of installation are important. They involve threading the end of the branch pipe and screwing it into a corresponding threaded opening on the main pipe. This creates a relatively simple and quick connection, requiring minimal tools and expertise. Think of them as the LEGOs of branch connections: easy to assemble, but not always the most robust.
Threaded connections are commonly used in residential plumbing and other low-pressure systems. They are relatively inexpensive and can be easily disassembled for maintenance or repairs. However, they are not as strong or leak-proof as welded connections and are not suitable for high-pressure or high-temperature applications. They're like that one friend who's always down for anything, but you wouldn't trust them to carry your expensive vase.
One potential downside of threaded connections is the risk of leaks. Over time, the threads can loosen or corrode, leading to leaks. To prevent this, it's important to use Teflon tape or pipe dope to seal the threads and ensure a tight connection. Regular inspection and maintenance are also crucial for preventing leaks and ensuring the long-term reliability of threaded connections.
Despite their limitations, threaded connections remain a valuable option for many applications. Their ease of installation and low cost make them a popular choice for situations where strength and durability are not paramount.
4. Mechanical Outlets
Mechanical outlets, also known as branch saddles, offer a versatile and flexible solution for creating branch connections without welding. They consist of a saddle-shaped fitting that clamps onto the main pipe, creating a secure and leak-proof connection. This makes them ideal for situations where welding is not feasible or desirable, such as when working with existing pipelines or in confined spaces. Think of them as the adaptable chameleons of branch connections: able to blend in and perform well in a variety of environments.
Mechanical outlets are available in a variety of sizes and materials, making them suitable for a wide range of applications. They can be used with different types of pipes, including steel, ductile iron, and plastic. They are also relatively easy to install, requiring minimal tools and expertise. They're like that handy gadget that can do just about anything, even open that stubborn jar of pickles.
One advantage of mechanical outlets is that they can be installed without interrupting the flow in the main pipe. This is particularly useful when working with live pipelines where shutting down the flow is not an option. However, it's important to follow the manufacturer's instructions carefully to ensure a proper and leak-proof installation. A poorly installed mechanical outlet can be a recipe for disaster.
While mechanical outlets may not be as strong as welded connections, they offer a convenient and versatile solution for many applications. Their ease of installation, flexibility, and ability to be installed on live pipelines make them a valuable tool for pipeline construction and maintenance.

BRANCH CONNECTION WELD FLANGES By Citizen Metals Issuu
Factors to Consider When Choosing a Branch Connection
5. Pressure and Temperature Ratings
One of the most important factors to consider when choosing a branch connection is its pressure and temperature ratings. The connection must be able to withstand the maximum pressure and temperature that the system will experience. Exceeding these ratings can lead to catastrophic failure, resulting in leaks, damage, and even injury. It's like trying to run a marathon without training — you're setting yourself up for failure (and a lot of pain).
Pressure and temperature ratings are typically specified by the manufacturer and should be clearly marked on the connection. It's important to choose a connection that has a safety margin to account for fluctuations in pressure and temperature. For example, if the system is expected to operate at a maximum pressure of 100 psi, it's best to choose a connection that is rated for at least 150 psi. Think of it as having a little extra gas in the tank — it's always better to be safe than sorry.
In addition to the pressure and temperature ratings of the connection itself, it's also important to consider the ratings of the pipe and other components in the system. The weakest link in the chain will determine the overall pressure and temperature limits of the system. A high-pressure connection is useless if the pipe it's connected to can't handle the same pressure.
When in doubt, it's always best to consult with a qualified engineer to ensure that the chosen branch connection is suitable for the intended application. They can help you assess the pressure and temperature requirements of the system and select a connection that meets those requirements. It's like having a personal trainer for your pipeline — they'll help you get it in top shape.
6. Material Compatibility
Another crucial factor to consider is the material compatibility between the branch connection and the pipes it will be connected to. Using incompatible materials can lead to corrosion, which can weaken the connection and eventually cause it to fail. This is particularly important when dealing with corrosive fluids or gases. It's like mixing oil and water — they just don't get along.
For example, if you're connecting a steel pipe to a copper pipe, you need to use a dielectric fitting to prevent galvanic corrosion. Galvanic corrosion occurs when two dissimilar metals are in contact in the presence of an electrolyte (such as water), creating an electrical current that corrodes one of the metals. A dielectric fitting isolates the two metals, preventing the flow of electrical current and preventing corrosion.
It's also important to consider the environment in which the connection will be installed. If the connection will be exposed to harsh chemicals or extreme temperatures, it's important to choose a material that is resistant to those conditions. Stainless steel, for example, is highly resistant to corrosion and is a good choice for applications where corrosion is a concern.
Consulting a materials specialist can be invaluable in selecting the right materials for your branch connections. They can help you identify potential compatibility issues and recommend materials that will provide long-term reliability and prevent corrosion. It's like having a personal chef who knows exactly which ingredients to combine to create the perfect dish — they'll help you avoid any culinary disasters.
7. Installation Considerations
The ease of installation is another important factor to consider when choosing a branch connection. Some connections, such as threaded connections, are relatively easy to install and require minimal tools and expertise. Others, such as welded connections, require skilled technicians and specialized equipment. It's like comparing IKEA furniture to custom-built cabinets — one is much easier to assemble than the other.
Consider the available space and accessibility when choosing a branch connection. If the connection will be installed in a confined space, a smaller and more compact connection may be necessary. If the connection will be difficult to access for maintenance or repairs, it's important to choose a connection that is durable and requires minimal maintenance. Think of it as choosing the right tool for the job — you wouldn't try to hammer a nail with a screwdriver, would you?
Proper installation is crucial for ensuring the long-term reliability of a branch connection. Always follow the manufacturer's instructions carefully and use the correct tools and techniques. A poorly installed connection can be a source of leaks, failures, and headaches down the road. It's like building a house on a shaky foundation — it's only a matter of time before it collapses.
If you're not comfortable installing a branch connection yourself, it's best to hire a qualified professional. They have the expertise and experience to ensure that the connection is installed correctly and safely. It's like hiring a professional electrician to wire your house — it's better to be safe than sorry.

What Are The Important Types Of Branch Pipe Connection?
Advanced Branch Connection Techniques
8. Reinforced Branch Connections
In high-pressure or critical applications, reinforced branch connections may be necessary to provide additional strength and prevent failure. Reinforced connections involve adding extra material around the branch opening to distribute the stress and prevent cracking. This can be achieved through various methods, such as using reinforcing pads or specially designed fittings. Think of them as the superheroes of branch connections, ready to withstand even the most extreme forces.
Reinforcing pads are typically welded around the branch opening to provide extra support. They are designed to distribute the stress evenly and prevent it from concentrating at the weld. The size and thickness of the reinforcing pad depend on the pressure and temperature requirements of the system. They're like wearing a bulletproof vest — providing an extra layer of protection against potential threats.
Specially designed fittings, such as integrally reinforced outlets (IROs), provide a more streamlined and efficient way to reinforce branch connections. IROs are manufactured with built-in reinforcement, eliminating the need for separate reinforcing pads. This simplifies the installation process and reduces the risk of errors. They're like having a suit of armor built right into your body — providing seamless and integrated protection.
The design and analysis of reinforced branch connections require specialized knowledge and expertise. It's important to consult with a qualified engineer to ensure that the reinforcement is adequate for the intended application. They can perform stress analysis and finite element analysis to determine the optimal reinforcement design. It's like having a team of engineers designing your superhero suit — ensuring that it's both functional and stylish.
9. Hot Tapping
Hot tapping, also known as pressure tapping, is a technique used to create a branch connection on a live pipeline without shutting down the flow. This is particularly useful when working with critical pipelines where interrupting the flow is not an option. Hot tapping involves welding a fitting onto the live pipeline, attaching a valve, and then using a special cutting tool to drill a hole through the pipe wall. Think of it as performing surgery on a patient who's still awake — requiring precision, skill, and a steady hand.
Hot tapping is a complex and potentially dangerous procedure that requires specialized training and equipment. It's important to follow strict safety procedures to prevent leaks, explosions, and other hazards. The pressure in the pipeline must be carefully monitored and controlled throughout the process. It's like defusing a bomb — one wrong move can have catastrophic consequences.
Before performing a hot tap, it's important to thoroughly inspect the pipeline to identify any potential weaknesses or defects. The pipe wall thickness must be sufficient to withstand the pressure and stress of the hot tapping process. If the pipe is corroded or damaged, it may be necessary to reinforce it before performing the hot tap. It's like giving the patient a thorough checkup before surgery — identifying any potential problems before they become serious.
Hot tapping is a valuable technique for maintaining and expanding pipeline networks without disrupting service. However, it should only be performed by qualified professionals who have the necessary training, experience, and equipment. It's not a DIY project for the faint of heart. Think of it as hiring a brain surgeon to remove a tumor — you wouldn't trust just anyone with such a delicate task.

Optimize Fluid Flow Branch Connections Guide By Citizen Pipe Fittings
FAQs About Branch Connections
10. What's the difference between a weldolet and a sockolet?
Good question! Both are types of welded outlets, but the main difference lies in how the branch pipe is connected. A weldolet is designed for butt-welded connections, meaning the branch pipe is directly welded end-to-end with the weldolet. This provides a smooth, strong connection. A sockolet, on the other hand, is designed for socket-welded connections, where the branch pipe is inserted into a socket in the sockolet and then welded. Sockolets are often easier to install but may not be as strong as weldolets.
11. Can I use a threaded connection for a gas pipeline?
That's a tricky one. While threaded connections can be used for some low-pressure gas applications, it's generally not recommended for high-pressure or critical gas pipelines. The risk of leaks is higher with threaded connections compared to welded connections. Always consult with a qualified engineer and local regulations to determine the appropriate type of connection for your specific gas pipeline application. Safety first!
12. How do I prevent leaks in a branch connection?
Leak prevention starts with choosing the right type of connection for the application and ensuring proper installation. For threaded connections, use Teflon tape or pipe dope to seal the threads. For welded connections, ensure proper welding techniques and inspect the welds for any defects. For mechanical outlets, follow the manufacturer's instructions carefully and ensure that the clamping force is adequate. Regular inspection and maintenance are also crucial for preventing leaks. Think of it as preventative medicine for your pipeline — taking care of it now can save you a lot of headaches (and leaks) down the road!
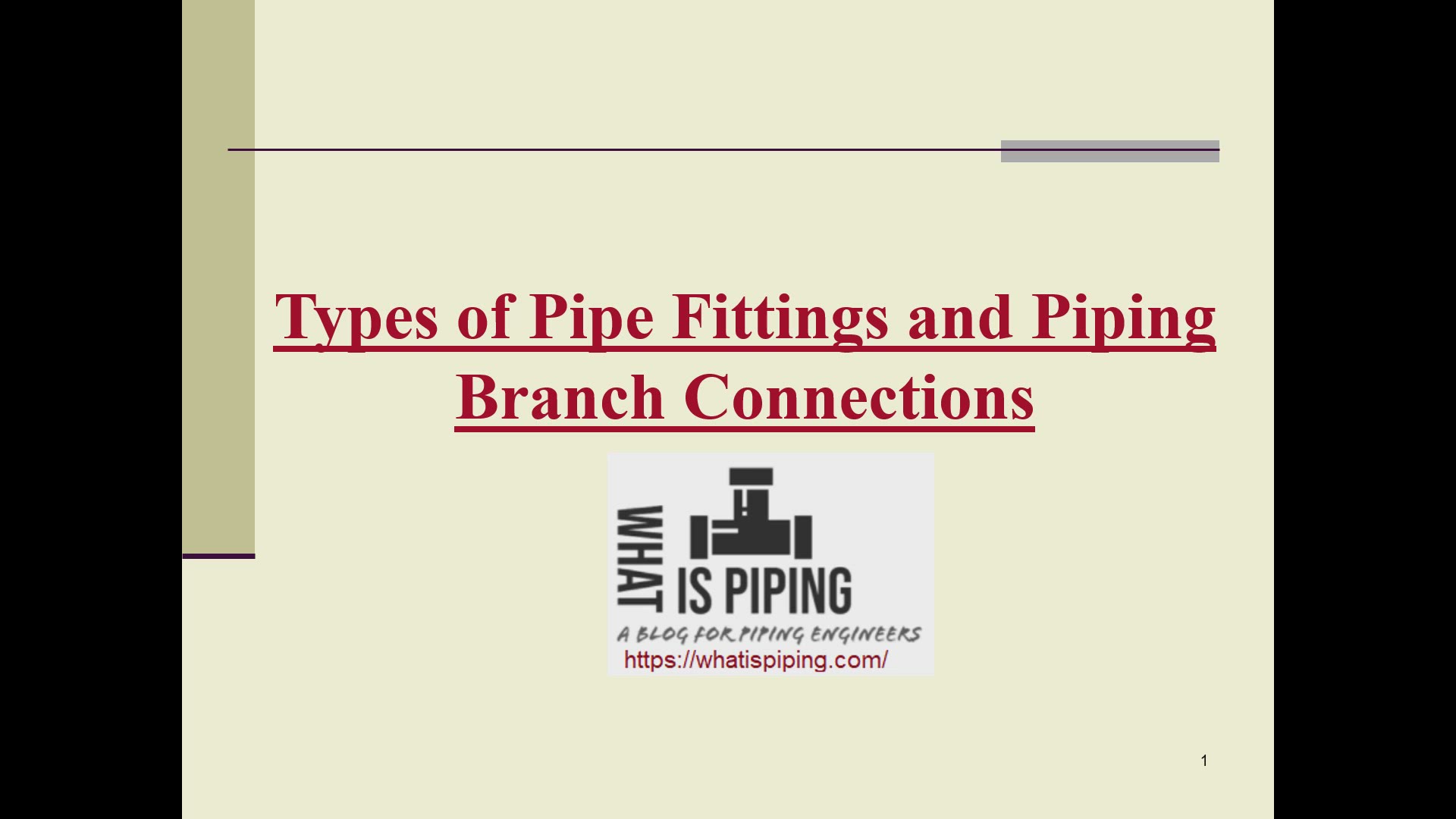