Supreme Info About Should I Use PWM Or DC
The DCDC Converter With Voltage Controller And PWM Signal
Decoding the Current
1. Understanding the Basics
Alright, let's dive into the electrifying world of power! Ever wondered whether Pulse Width Modulation (PWM) or Direct Current (DC) is the better choice for your project? It's a common head-scratcher, and honestly, the answer isn't always a simple yes or no. Think of it like choosing between a Swiss Army knife and a specialized screwdriver. Both can handle screws, but one is more versatile while the other excels in a specific situation.
DC, or Direct Current, is like a calm, steady river flowing in one direction. It's what you get from batteries and most power adapters. Imagine it as a constant stream of electrons happily marching along. Simple, reliable, and straightforward. You flip a switch, and power flows. You flip it again, and it stops. No fuss, no muss.
PWM, on the other hand, is a bit more sophisticated. It's like a tap that turns on and off very, very quickly. The 'pulse width' refers to how long the tap is on compared to how long it's off. By varying this width, you can effectively control the amount of power delivered to a device. Imagine dimming a lightbulb — thats PWM in action! It's quick on-off cycles create the illusion of a lower voltage, while using full available power when it is on.
So, we have the steady flow of DC and the rapid on-off cycles of PWM. Ready to see where each shines?
2. Where DC Dominates
DC is the champion for situations where you need a constant, unwavering source of power. Think of applications where consistency is key. For example, powering a simple LED is often best done with DC. The LED needs a certain voltage to light up, and providing that directly with DC ensures a stable, consistent brightness. No flickering, no surprises, just pure, unadulterated light.
Another great example is powering sensitive electronics. Many microcontrollers and sensors rely on a clean, steady DC voltage to operate correctly. Fluctuations or interruptions in power can cause them to malfunction or even be damaged. A regulated DC power supply provides that much-needed stability, ensuring reliable operation. It's like giving your electronics a nice, smooth cup of tea instead of a jolting energy drink.
Furthermore, for certain motor applications requiring a very specific RPM, DC coupled with a feedback loop can be more easily controlled than PWM at very low duty cycles. The constant voltage makes prediction of motor speed far more precise.
In essence, DC is the go-to choice when you need simplicity, reliability, and a stable, predictable power source. Think of it as the trusty old workhorse that gets the job done without any fancy frills.
3. The PWM Power Play
Now, let's talk about PWM's strengths. Where DC provides a steady stream, PWM offers precise control. Its ability to rapidly switch power on and off allows for incredibly nuanced adjustments. This makes it perfect for applications where you need to fine-tune the amount of power delivered.
One of the most common uses of PWM is to control the speed of motors. By varying the pulse width, you can effectively adjust the voltage supplied to the motor, thereby controlling its speed. Imagine a remote-controlled car. PWM allows you to gently accelerate, smoothly cruise, and powerfully brake, all with precise control over the motor's speed. It's like having a volume knob for your motor!
Another area where PWM excels is in dimming LEDs. While you can dim LEDs with DC by reducing the voltage, this can lead to changes in color temperature and reduced efficiency. PWM, on the other hand, maintains the color temperature while effectively dimming the LED. It's like turning down the brightness on your phone — the colors stay true, just less intense.
PWM is also more efficient than DC voltage regulation for many applications. Because the switching transistors are either fully on or fully off, very little power is wasted as heat compared to dropping voltage with a resistor or linear regulator. This is particularly important when dealing with battery-powered devices where conserving energy is paramount.
4. Efficiency Face-Off
Often, PWM comes out ahead when we're talking efficiency. Let's say you want to dim an LED using DC. You could use a resistor to drop the voltage, but that resistor turns the excess energy into heat. That's wasted power! PWM, however, rapidly switches the power on and off. When it's off, no power is consumed. When it's on, it's using full power, but only for a fraction of the time. This drastically reduces the overall power consumption, making PWM much more efficient.
Consider controlling a motors speed. With DC, you could lower the voltage, but again, that's often done inefficiently, wasting energy as heat. PWM delivers power in short bursts. When the motor needs less speed, the bursts are shorter, conserving energy. It's like gently tapping the gas pedal in your car instead of constantly flooring it.
This efficiency is critical in battery-powered applications. Think of a drone, where every milliwatt of power matters. Using PWM to control the motors and other components extends the flight time significantly compared to using inefficient DC voltage regulation. It's the difference between a quick buzz around the park and a longer, more enjoyable flight.
So, if you're looking to save energy and extend battery life, PWM is generally the more efficient choice. While DC can be made more efficient with specialized regulators, PWM often offers a simpler and more cost-effective solution.
5. Making the Right Choice
Alright, so how do you actually decide whether to use PWM or DC for your specific project? Here's a breakdown:
1. Consider the application: What are you trying to power or control? If it's something simple that requires a constant, unwavering power source (like a basic LED or a simple circuit), DC is likely the way to go. If you need precise control over power delivery (like motor speed or LED brightness), PWM is probably the better choice.
2. Think about efficiency: Is power consumption a major concern? If you're working with battery-powered devices or anything where energy conservation is critical, PWM is generally the more efficient option.
3. Assess the complexity: DC is generally simpler to implement. It often requires just a power source and a switch. PWM requires a bit more circuitry to generate the pulse width modulated signal. However, many microcontrollers have built-in PWM capabilities, making it relatively easy to implement.
4. Factor in cost: DC power supplies are often cheaper and more readily available than dedicated PWM controllers. However, the added efficiency of PWM can sometimes offset the initial cost, especially in the long run.Ultimately, the best choice depends on the specific requirements of your project. There's no one-size-fits-all answer, so carefully weigh the pros and cons of each option before making a decision. Its also a good idea to prototype and test your circuit with both methods to see which performs better in practice!

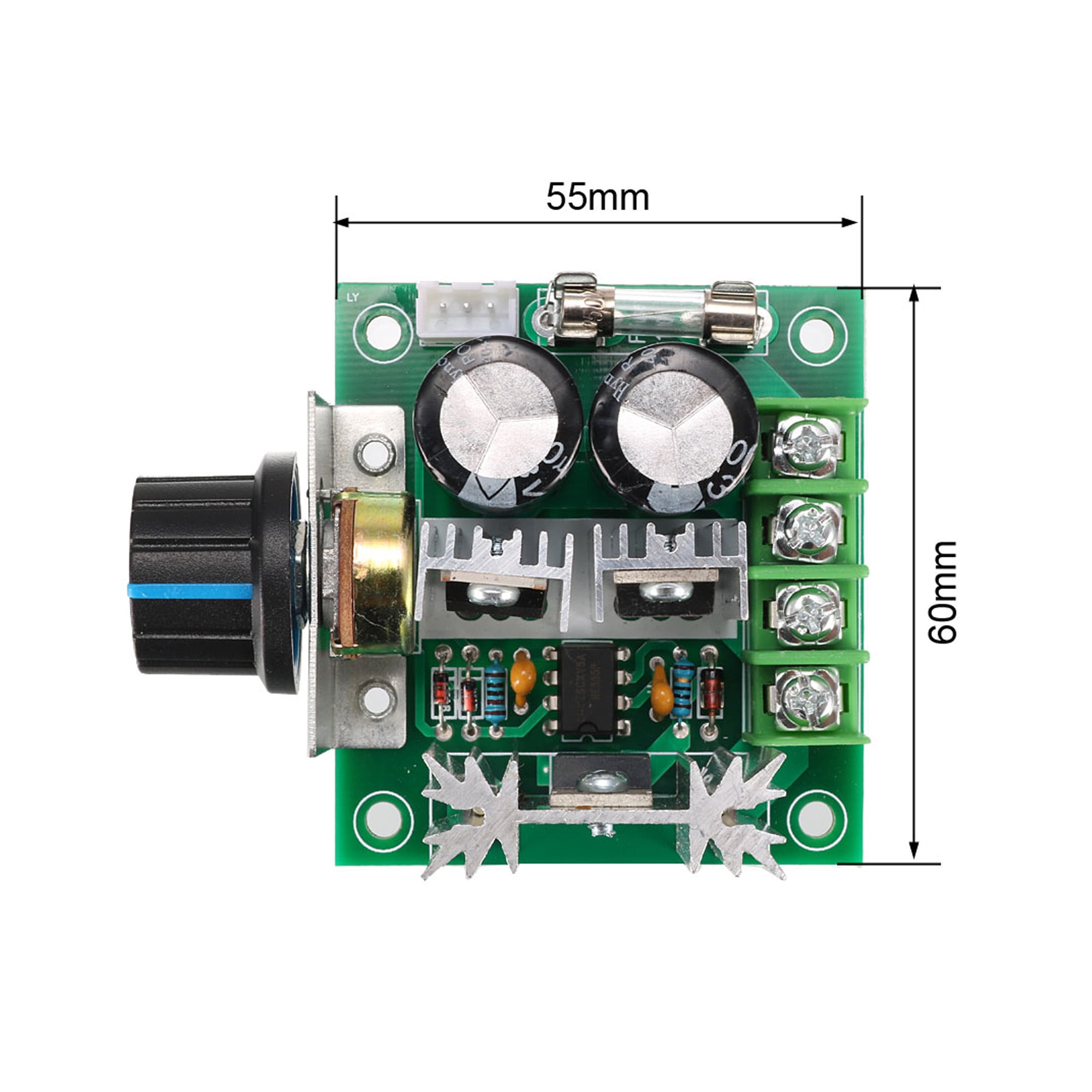
Autres Equipement électrique, Fournitures 12V40V 10A Pulse Width

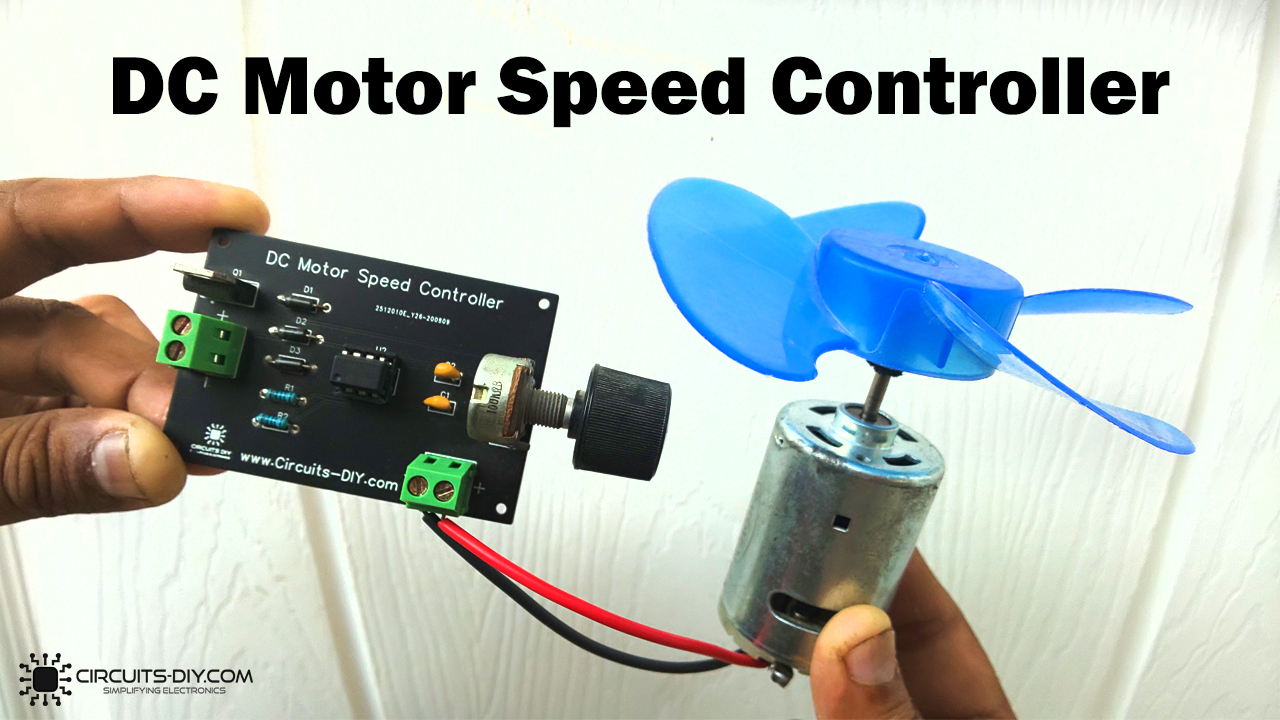
DC Motor Speed Controlling Circuit PWM
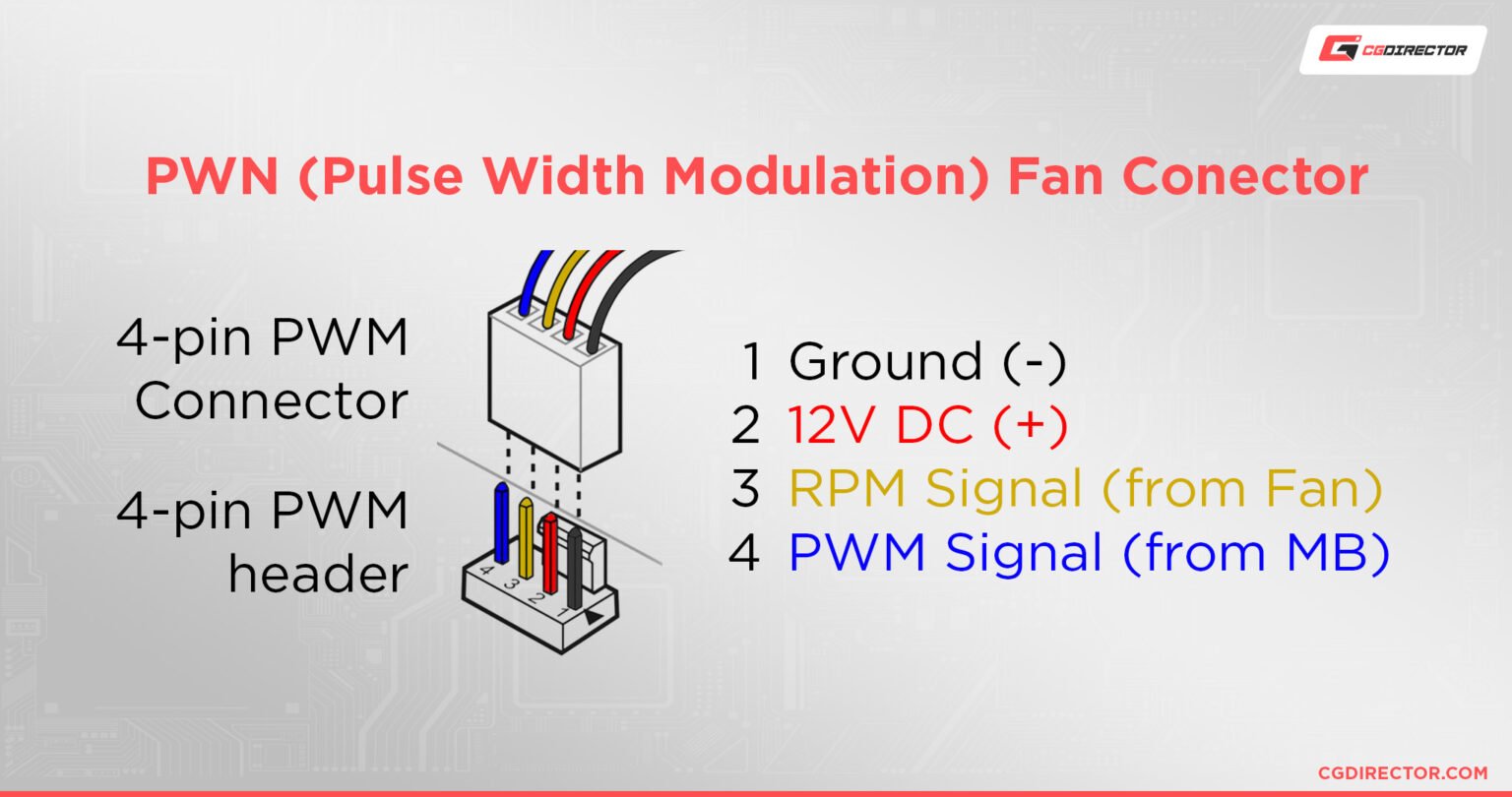