Impressive Tips About Does Flux Help Melt Solder
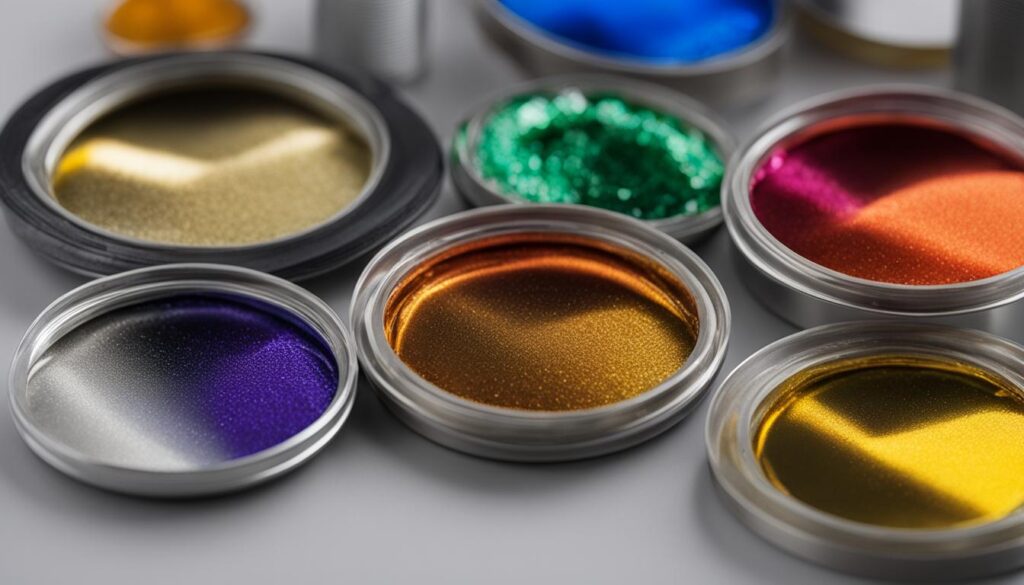
The Solder Saga
1. Unveiling the Mystery of Flux
So, you're wrestling with solder, huh? It's behaving like a toddler refusing vegetables, just not cooperating. The question on your mind is, "Does flux help melt solder?" Let's get straight to the point: Absolutely! But it's not just about the melting. Think of flux as the unsung hero, the behind-the-scenes magician that makes the whole soldering process smoother than a freshly paved road.
But why? What's the magic behind this mysterious substance? Well, soldering isn't just about applying heat. It's about creating a strong, clean connection between two metal surfaces. The problem is, those metal surfaces are often covered in a microscopic layer of oxides and other contaminants. These impurities act like a stubborn gatekeeper, preventing the solder from properly bonding.
That's where flux swoops in to save the day. Flux is designed to chemically clean those surfaces. When heated, it melts and removes those pesky oxides, creating a pristine surface for the solder to adhere to. Without flux, you're basically trying to glue two dusty surfaces together — it's just not going to work well, if at all.
Consider flux like the pre-wash cycle for your clothes. It lifts the grime, allowing the detergent (in this case, the solder) to really get in there and do its job. A good flux ensures that the melted solder flows evenly and wets the metal surfaces properly, resulting in a strong and reliable joint. Think of it as the difference between a flimsy handshake and a solid, confident grip.
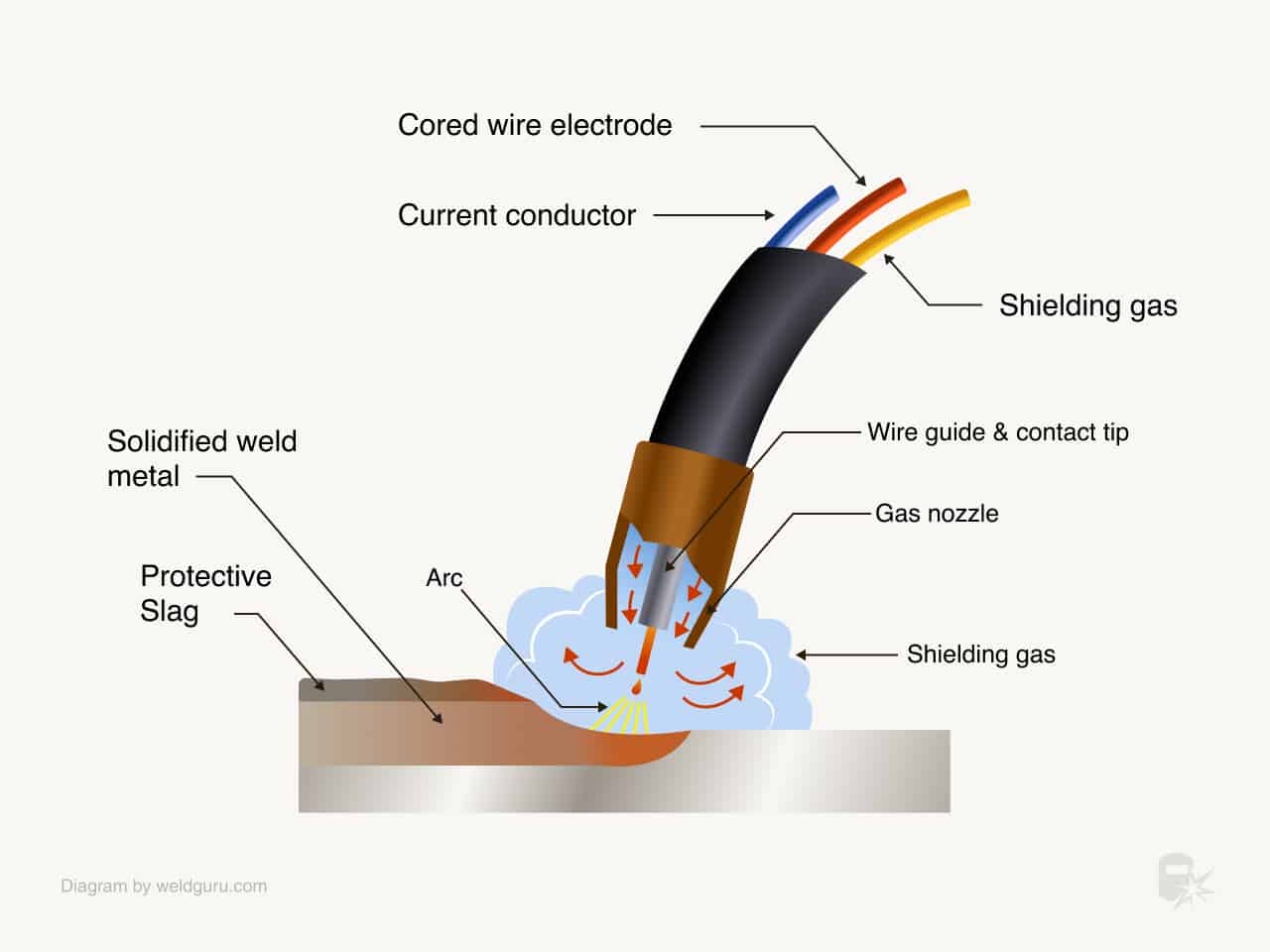
What Is FluxCore Arc Welding (FCAW) How Does It Work?, 44 OFF
The Science Behind the Sizzle
2. Delving Deeper into Flux Functionality
Okay, we know flux helps, but let's peek under the hood and understand how it actually accomplishes this feat. It's not just some random chemical goo, after all. There's some pretty neat science at play here. The core function of flux, as we touched upon, is oxide removal. Oxides are compounds formed when metal reacts with oxygen in the air. They're like the rust on your old bicycle, but on a much smaller, microscopic scale.
Different types of flux contain different chemical compounds, each with its own specific melting point and reactivity. When the flux is heated, these compounds react with the metal oxides, converting them into other substances that can be easily displaced by the molten solder. Some fluxes even create a temporary protective barrier, preventing further oxidation from occurring during the soldering process.
Think of it like a tiny army of microscopic cleaners, scrubbing away all the dirt and grime on the metal surface. As the solder melts, it flows over the cleaned surface, creating a strong metallic bond. This bond is crucial for ensuring a reliable electrical or mechanical connection. Without flux, the solder would simply ball up and sit on top of the oxides, creating a weak and unreliable joint. Imagine trying to build a house on a foundation of loose sand — it's not going to end well.
The type of flux you use also matters. Rosin-based fluxes are commonly used in electronics due to their relatively mild activity and ease of cleaning. Acid fluxes, on the other hand, are more aggressive and are typically used for soldering metals like copper and steel. Choosing the right flux for the job is essential for achieving a successful solder joint.

Flux Types
3. Navigating the Fluxiverse
So, weve established that flux is important. But hold on, before you grab the first jar of gloop you see, lets talk types. It's not a one-size-fits-all situation. The world of flux is surprisingly diverse, each type tailored for specific soldering applications. Knowing your flux types is like knowing the different spices in your kitchen — it allows you to create the perfect blend for your specific needs.
First up, we have Rosin Flux. This is your go-to for electronics work. It's relatively mild, cleans well, and the residue isn't very corrosive. You'll often find it in a solid form or as a liquid. Rosin fluxes are generally classified as RMA (Rosin Mildly Activated), RA (Rosin Activated), and RSA (Rosin Super Activated), with increasing levels of activity. For hobbyist electronics, RMA is usually a safe bet.
Next, we have Acid Flux. This stuff is the heavy-duty cleaner. Think of it as the industrial-strength detergent of the soldering world. It's used for soldering metals like copper, steel, and even some stainless steels. However, it's also highly corrosive, so you need to clean it off thoroughly after soldering. If you don't, it can corrode your connections over time. Acid fluxes are definitely not recommended for electronics due to their corrosive nature.
Then there's No-Clean Flux. The name says it all, right? These fluxes leave behind a residue that's considered non-corrosive and doesn't need to be cleaned off. They're popular in high-volume manufacturing where cleaning can be time-consuming. However, some no-clean fluxes can still leave a slightly tacky residue, which might not be ideal for all applications. Always check the manufacturer's recommendations.
And finally, a mention for Water-Soluble Flux. As you might guess, these fluxes can be cleaned off with water. They tend to be more aggressive than rosin fluxes, making them suitable for soldering difficult-to-solder metals. They are however, corrosive if left on the board, so make sure you clean them off with distilled water after your done soldering.
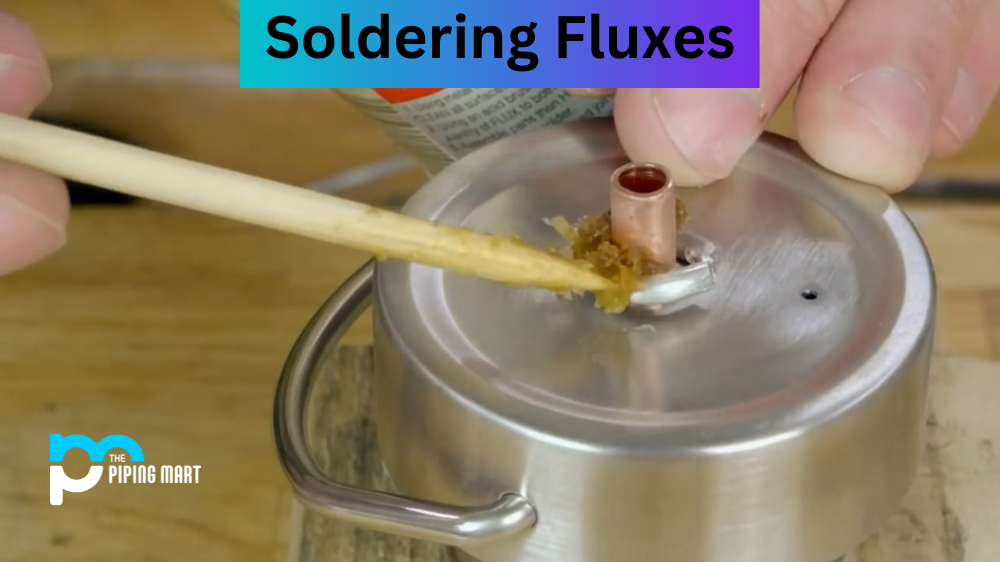
Soldering Flux Do At Robert Locklear Blog
Applying Flux Like a Pro
4. Mastering the Art of Flux Application
So, you've chosen your flux, you have your solder. Now what? Just slather it on like peanut butter? Not quite. Applying flux correctly is just as important as choosing the right type. A little finesse goes a long way. The goal is to apply enough flux to clean the surfaces without overdoing it and making a mess. Think of it like seasoning your food — a pinch enhances the flavor, but too much can ruin the dish.
If you're using a liquid flux, a small brush or a flux pen is your best friend. Apply a thin, even layer of flux to the surfaces you're going to solder. Avoid getting flux on areas you don't intend to solder, as it can make a mess and potentially cause corrosion. If you're using a solid flux, you can either apply it directly to the solder or to the workpiece. Some solder already contains a core of flux — this is called core solder — making the process even simpler.
The amount of flux you need will depend on the size of the joint and the condition of the metal surfaces. If the surfaces are heavily oxidized, you might need to apply a bit more flux. However, it's always better to err on the side of caution and apply too little than too much. You can always add more flux if needed, but it's much harder to remove excess flux.
One common mistake is overheating the flux. If you apply too much heat too quickly, the flux can burn and become ineffective. The ideal temperature for fluxing is just below the melting point of the solder. This allows the flux to clean the surfaces without burning. A good rule of thumb is to apply the heat gradually and observe the flux as it melts. You'll see it bubbling and cleaning the metal surfaces. This is a good sign that it's working properly.
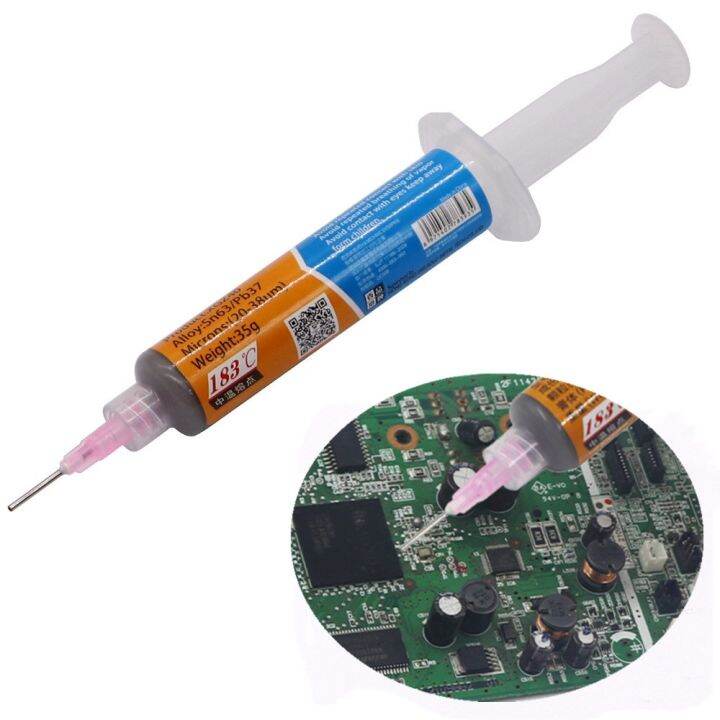
Common Flux Fails and How to Avoid Them
5. Troubleshooting Your Fluxing Adventures
Even with the best intentions, things can sometimes go awry. Maybe your solder joint looks like a cold, lumpy mess, or maybe your connections are failing prematurely. In some cases, the most likely culprit is flux-related. Knowing the common pitfalls can save you a lot of time and frustration. Think of this as your troubleshooting guide to the world of flux.
One of the most common mistakes is using the wrong type of flux. As we discussed earlier, different fluxes are designed for different applications. Using an acid flux on electronics, for example, is a recipe for disaster. Always double-check the manufacturer's recommendations and choose the flux that's appropriate for your specific soldering task.
Another common issue is insufficient flux. If you don't apply enough flux, the solder won't properly wet the metal surfaces, resulting in a weak and unreliable joint. This can happen if the surfaces are heavily oxidized or if you're using a flux with low activity. If you suspect this is the problem, try applying a bit more flux or switching to a more active flux.
Overheating the flux is another common pitfall. If you apply too much heat too quickly, the flux can burn and become ineffective. This can also happen if you're using a flux with a low boiling point. The best way to avoid this is to apply the heat gradually and observe the flux as it melts. If you see it smoking or turning black, you're probably overheating it.
Finally, failing to clean the flux residue can also cause problems. While some fluxes are designed to be no-clean, others can leave behind a corrosive residue that can damage your connections over time. Always clean the flux residue thoroughly after soldering, especially if you're using an acid flux. Isopropyl alcohol or specialized flux removers can be used for this purpose. A clean joint is a happy joint!
