Nice Tips About Does A Motor Run Faster In Star Or Delta

Decoding the Star-Delta Mystery
1. Unraveling the Connections
So, you're wondering if your motor suddenly transforms into a speed demon when switched between star (Y) and delta (Δ) configurations? Well, let's dive into this electrical engineering puzzle! The short answer: a motor doesn't inherently run faster in one configuration versus the other. The key is understanding how these configurations affect voltage and current, and how that relates to a motor's torque and intended operating parameters. Think of it like this: it's not about the outfit, it's about the power source!
Imagine a motor as a well-trained athlete. It has a specific range where it performs optimally. Star and delta configurations are simply different ways of connecting that athlete to the power grid, ensuring it gets the right "nutrients" (voltage and current) to perform its best. Misfeeding it can lead to underperformance or even burnout! Therefore, choosing the right configuration is less about raw speed, and more about whether you want the machine to start slowly (star) or run at its full capacity (delta) without damaging components.
The shift from star to delta is a carefully orchestrated dance. When you initially switch on a motor in star configuration, it receives a reduced voltage across each winding. This limits the starting current, preventing a massive surge that could trip breakers and cause all sorts of electrical mayhem. Once the motor reaches a certain speed, it transitions to the delta configuration, applying the full line voltage and allowing it to operate at its rated speed and power. It's like giving the athlete a gradual warmup before unleashing them on the track.
Think of star as 'soft start' mode. Delta is the full power mode. They don't inherently change speed; they just control how the motor ramps up to its designed operating speed under its specific load. It is important to pick one which makes your motor working with the maximum efficiency under normal running conditions, without over heating or causing a failure to the motor or attached load. Its not magic, its all about respecting the motors design!
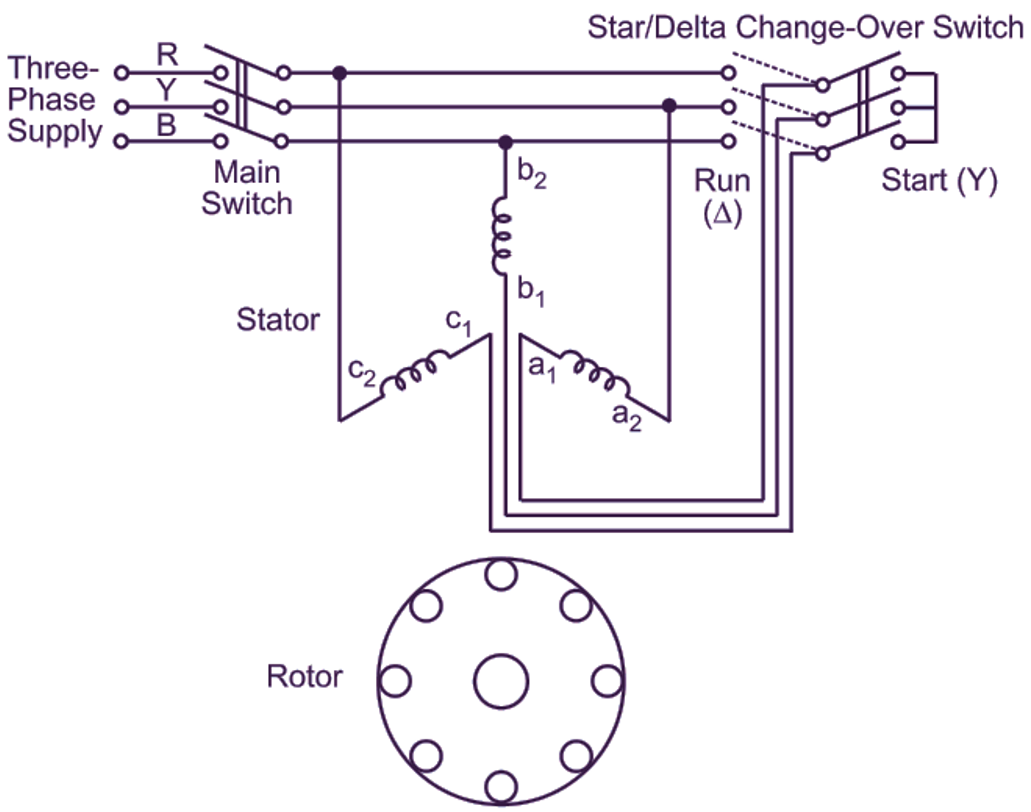
What Is Star Delta Starter? Working & Diagram ElectricalWorkbook
Voltage, Current, and the Motor's Sweet Spot
2. Voltage's Crucial Role
Lets break down the nitty-gritty (oops, almost slipped up!) of voltage and current in each configuration. In a star connection, the voltage across each motor winding is equal to the line voltage divided by the square root of 3 (approximately 1.732). This reduced voltage leads to a lower starting current — typically about one-third of the current it would draw if started directly in delta. Lower current means less stress on the power grid and the motor itself during startup.
Now, let's switch gears to delta. In this configuration, the full line voltage is applied directly across each motor winding. This means the motor can deliver its full rated torque and power. However, it also means a higher inrush current during startup. That's why you typically use star-delta starters for larger motors: to gently nudge them into operation before unleashing their full potential.
The relationship between voltage, current, and motor speed is complex but fundamental. A motor's speed is primarily determined by the frequency of the power supply and the number of poles in the motor's winding. However, voltage plays a critical role in torque production. Lower voltage means lower torque, which can affect the motor's ability to accelerate and maintain its speed under load. Get the voltage wrong and the motor won't deliver what is expected, perhaps start to vibrate, get hot and then possibly fail. Don't be that guy!
It is important to match the voltage rating of the motor with that of the power supply. Motors are designed to operated at the rated voltage. If the voltage applied is less than this value, then the motor can still be used, but it will produce less torque. If the voltage applied exceeds the rated voltage then the motor is likely to fail. Therefore, motors are fitted with an overload device which will switch off the motor if too much current is being drawn.

Star Delta Connection In Motor Terminal Block
Star-Delta Starting
3. Controlling the Initial Rush
Think of star-delta starting as a clever trick to soften the blow of a motor starting up. Direct-on-line (DOL) starting, where you just flip the switch and the motor roars to life, is fine for smaller motors. But for larger ones, the inrush current can be enormous, potentially causing voltage dips in the entire electrical system. Imagine your lights dimming every time the fridge kicks on that's the kind of disruption we're trying to avoid!
Star-delta starting reduces this inrush current by initially connecting the motor windings in a star configuration. This effectively reduces the voltage applied to each winding, limiting the current. Once the motor reaches a certain speed (typically around 80% of its rated speed), a timer switches the configuration to delta, applying the full line voltage. This allows the motor to operate at its full rated power without causing a massive surge on the power grid. It is like easing into a hot tub gently rather than jumping straight in.
The transition from star to delta is crucial. It needs to be smooth and quick to avoid a "glitch" in the motor's operation. A poorly timed transition can cause a momentary drop in speed and torque, which can be detrimental to the driven equipment. Properly sized contactors and a well-configured timer are essential for a reliable star-delta starting system.
Without this clever technique, it would be like trying to accelerate from 0 to 60 mph in first gear — incredibly inefficient and potentially damaging. Star-delta starting allows a motor to gather momentum gradually, like shifting gears smoothly to reach top speed. It ensures the equipment starts to run reliably, without causing damage.
The Motor Should Run On Star Connection Or Delta Connection?
Beyond Speed
4. More Than Just RPMs
While the primary focus is often on motor speed, it's crucial to remember that torque and load play equally important roles in determining the overall performance of a motor. Torque is the rotational force that the motor produces, and it's directly related to the voltage and current applied to the windings. A motor with high torque can handle heavier loads without slowing down significantly. So, while the motor itself may not run faster in delta, it will be capable of running at its designed speed under a heavier load compared to the star configuration (before the switch).
The load connected to the motor is another critical factor. A lightly loaded motor will accelerate quickly and reach its rated speed relatively easily. However, a heavily loaded motor will take longer to reach its rated speed and may even struggle to reach it at all if the applied voltage is insufficient. That's why it's important to carefully consider the load characteristics when selecting a motor and its starting method. It is important to choose a motor with the correct characteristics, so it works efficiently in the operating environment.
Efficiency is also a key consideration. A more efficient motor will convert a larger percentage of electrical energy into mechanical energy, reducing energy waste and saving money. Motors operating at their rated voltage and load tend to be most efficient. Running a motor at a reduced voltage (as in the star configuration) can decrease its efficiency, especially if it's heavily loaded. Efficiency is very important to reduce the energy usage of a machine and reduce the impact on the environment.
Therefore, you should pick the best motor for your application, install and commission it correctly. Regularly perform maintenance, to keep the motor operating efficiently. Also check for signs of damage to the motor, such as overheating, vibration, and unusual noises. Any one of these may indicate a problem that could cause damage to the motor if not fixed.

Motor Starters Part 3 Pros And Cons Of The StarDelta Configuration
Star vs. Delta
5. Matching the Motor to the Job
So, when do you choose star and when do you choose delta? Star configuration is generally used for starting large motors to reduce the starting current. This is particularly useful in applications where the power supply is weak or where there are other sensitive equipment connected to the same power grid. Delta configuration, on the other hand, is used for running the motor at its full rated power once it has reached a certain speed. It's like choosing the right gear in a car — you start in a lower gear (star) to get moving, and then shift to a higher gear (delta) for cruising speed.
The decision of whether to use star-delta starting depends on several factors, including the size of the motor, the characteristics of the load, and the capacity of the power supply. Smaller motors can often be started directly on line (DOL) without causing significant voltage dips. However, larger motors typically require some form of reduced voltage starting, such as star-delta, auto-transformer, or soft starter. Without this voltage reduction, large currents can flow in the system, leading to the failure of components.
Ultimately, the choice between star and delta comes down to optimizing the motor's performance for its specific application. It's not about making the motor run faster, but about ensuring that it starts smoothly, operates efficiently, and delivers the required torque to drive the load without causing electrical disturbances. Matching the starting method to the motor and load is critical for reliability and longevity.
Always consult the motor's nameplate and the manufacturer's recommendations when deciding on the appropriate starting method. Incorrectly configuring a motor can lead to overheating, reduced lifespan, and even catastrophic failure. It is important that the motor is matched to the supply correctly. Incorrect wiring may lead to the equipment overheating and causing a fire.

In Which Connection Does A Motor Run Fast, Star Or Delta?
Frequently Asked Questions (FAQs)
6. Addressing Your Burning Questions
Alright, let's tackle some common questions about star and delta configurations:
Q: Can I convert a motor from star to delta while it's running?A: That's exactly what star-delta starters do! They automatically switch from star to delta once the motor reaches a certain speed. Doing it manually would be tricky and potentially damaging, so stick with the automated systems.
Q: What happens if I run a motor in star configuration continuously?A: You can run a motor in star continuously, but it won't deliver its full rated power. It will produce less torque, and its efficiency may be reduced. It's like driving a car in second gear all the time — you'll get there eventually, but it won't be pretty.
Q: Is star-delta starting suitable for all types of motors?A: No, star-delta starting is primarily used for induction motors designed to be run in delta. It's not appropriate for all motor types. Always check the motor's nameplate and the manufacturer's instructions to ensure compatibility.
Q: My motor is rated 400V Delta / 690V Star, what does this mean?A: It means that when wired in a delta configuration the motor needs to be supplied with a 400V supply. When wired in star configuration the motor is suitable for use with a 690V supply. You must not wire it as delta and give it 690V as this will cause damage to the winding and cause failure of the motor.