Here's A Quick Way To Solve A Tips About Can You Solder Without Flux

The Sticky Truth About Solder
1. Why Flux is Generally Your Soldering Buddy
So, you're staring at your soldering iron, some wire, and a roll of solder, and you're thinking, "Do I really need that flux stuff?" It's a fair question. Flux, that slightly smelly paste or liquid, seems like an extra step, right? Well, let's get straight to the point: soldering without flux is generally a recipe for frustration, cold solder joints, and maybe even a little colorful language. But why?
Think of it this way: metal surfaces, even the ones that look shiny and new, are covered in a microscopic layer of oxidation. This oxidation is like a stubborn shield, preventing the solder from properly bonding with the metal. The solder needs direct contact with the clean metal surface to form a strong, electrically conductive joint. Without flux, the solder will likely just bead up and roll around, refusing to stick properly. It's like trying to glue something to a greasy surface — not gonna happen!
Flux acts like a chemical cleaner, removing that pesky oxidation and allowing the molten solder to flow freely and "wet" the metal surfaces. This wetting action is crucial for creating a solid metallurgical bond. The flux also protects the cleaned surfaces from further oxidation during the heating process. It's basically a bodyguard for your solder joint.
Therefore, while technically, you might get away with soldering without flux in some very specific, controlled situations (we'll get to those later), it's almost always a bad idea. It's like trying to bake a cake without baking powder: you might end up with something vaguely resembling a cake, but it won't be pretty, and it probably won't taste very good.
When Might You Consider Skipping Flux? (Keyword: Solder)
2. Rare Exceptions, Not the Rule
Okay, I've painted a pretty dire picture of soldering without flux, and honestly, I stand by it. However, there are a few very specific circumstances where you might be able to get away without it, or where the flux is already integrated into the solder itself. But remember, these are exceptions, not the rule. Treat them with caution!
One instance is when using solder that has a flux core. This type of solder has the flux built right into the center of the wire. As the solder melts, the flux is released, cleaning the surfaces as you solder. However, even with flux-core solder, it's often a good idea to add a little extra flux, especially if you're working with heavily oxidized or tarnished materials. Think of it as extra insurance.
Another (extremely rare) scenario is if you are soldering pristine, freshly cleaned surfaces in an inert atmosphere (like a nitrogen-filled chamber). In this controlled environment, oxidation is minimized, and you might be able to get away with soldering without additional flux. But let's be honest, unless you're working in a high-tech lab, this probably doesn't apply to you. And even then, many professionals would still use flux for added assurance.
Finally, some specialized soldering applications, like wave soldering in mass production, might use specific cleaning processes that negate the need for individual flux application. However, these are highly specialized industrial processes and are far removed from the typical DIY or hobbyist soldering scenarios.

The Downside of "Going Commando" (No Flux Soldering)
3. The Price of Neglecting Flux
Let's delve a little deeper into why skipping the flux is generally a bad idea. It's not just about making the soldering process slightly more difficult; it's about the quality and reliability of your solder joints. A cold solder joint, which is a common consequence of soldering without flux, is a weak and unreliable connection. It might look okay on the surface, but it's prone to cracking, corrosion, and eventual failure. Imagine building a house with poorly mixed concrete — it might stand for a while, but eventually, it's going to crumble.
Cold solder joints often have a dull, grainy appearance, rather than the shiny, smooth look of a properly soldered joint. This visual cue can be helpful in identifying potential problems. Electrically, cold solder joints can cause intermittent connections, signal degradation, and even complete circuit failure. This can be incredibly frustrating, especially if you've spent hours troubleshooting a complex electronic device.
Furthermore, attempting to solder without flux can lead to overheating the components you're trying to join. Because the solder isn't flowing properly, you're likely to apply more heat in an attempt to get it to stick. This excessive heat can damage sensitive electronic components, rendering them useless. It's like trying to force a square peg into a round hole — you're just going to end up breaking something.
In short, the time and effort you save by skipping the flux are often far outweighed by the potential problems and rework required to fix poorly soldered joints. It's always better to do it right the first time, even if it means taking an extra step.

Choosing the Right Flux
4. Picking Your Poison (The Safe Kind, Of Course)
Okay, you're convinced: flux is essential for good soldering. But with so many different types of flux available, how do you choose the right one for your project? The answer depends on the materials you're soldering and the specific application.
For electronics work, rosin-based fluxes are generally the most popular choice. Rosin flux is mildly acidic and effectively removes oxidation without being overly corrosive to delicate electronic components. It's also relatively easy to clean up after soldering, either with isopropyl alcohol or specialized flux removers.
For plumbing or other non-electronic applications, acid fluxes are often used. Acid fluxes are more aggressive than rosin fluxes and are better at removing heavy oxidation and corrosion from metals like copper and steel. However, acid fluxes are highly corrosive and must be thoroughly cleaned off after soldering to prevent future corrosion.
No-clean fluxes are also available, which are designed to leave a minimal residue after soldering. While these fluxes can be convenient, it's still a good idea to inspect the solder joint after soldering to ensure that there are no corrosive residues present. In some cases, even "no-clean" fluxes may require some cleaning, especially in high-reliability applications.
When in doubt, consult the product documentation or ask a professional for advice. Choosing the right flux can make a significant difference in the quality and reliability of your solder joints.

Soldering Best Practices
5. Tips for a Successful Soldering Experience
Now that you understand the importance of flux, let's talk about some general soldering best practices to ensure a successful and enjoyable experience. First and foremost, always work in a well-ventilated area. Flux fumes can be irritating and potentially harmful, so it's important to have good airflow to dissipate them. A small fan can be helpful in directing fumes away from your face.
Before soldering, thoroughly clean the surfaces you're going to join. Use sandpaper, steel wool, or a specialized cleaning solution to remove any dirt, grease, or heavy oxidation. This will help the flux do its job more effectively and ensure a strong bond.
Apply a thin, even layer of flux to the surfaces you're soldering. Don't overdo it; too much flux can actually hinder the soldering process. A small amount of flux goes a long way. Heat the joint evenly, and apply the solder to the joint, not directly to the soldering iron tip. The heat from the joint will melt the solder, and the flux will help it flow smoothly and evenly.
After soldering, allow the joint to cool naturally. Avoid blowing on it or quenching it with water, as this can weaken the joint. Once the joint has cooled, inspect it carefully to ensure that it's shiny, smooth, and free of any cracks or voids. If necessary, clean off any flux residue with isopropyl alcohol or a specialized flux remover.
Remember, practice makes perfect. Don't be discouraged if your first few solder joints aren't perfect. With a little patience and persistence, you'll soon be soldering like a pro.

FAQ
6. All About Solder
Q: Can I use toothpaste as a substitute for flux?
A: Absolutely not! Toothpaste is not designed for soldering and contains ingredients that can contaminate the joint and prevent a proper bond. It might seem like a fun experiment, but trust me, it's not worth the potential damage to your components.
Q: What happens if I use too much flux?
A: While flux is essential, using too much can also be problematic. Excessive flux can leave behind corrosive residues that can damage electronic components. It can also make it difficult to see the solder joint properly. If you use too much flux, clean it off thoroughly after soldering.
Q: Is there a "best" type of flux for all soldering applications?
A: No, there's no one-size-fits-all flux. The best type of flux depends on the materials you're soldering and the specific application. Rosin flux is generally a good choice for electronics work, while acid flux is better for plumbing and other non-electronic applications. Consult the product documentation or ask a professional for advice if you're unsure which flux to use.
Q: What if my solder isn't sticking, even with flux?
A: If your solder isn't sticking, even with flux, there could be several reasons. The surfaces you're soldering might not be clean enough. The soldering iron might not be hot enough. You might not be applying the solder to the joint properly. Or, the flux might be old or ineffective. Try cleaning the surfaces more thoroughly, increasing the soldering iron temperature, and using fresh flux. If all else fails, consult a soldering guide or seek help from a more experienced solderer.
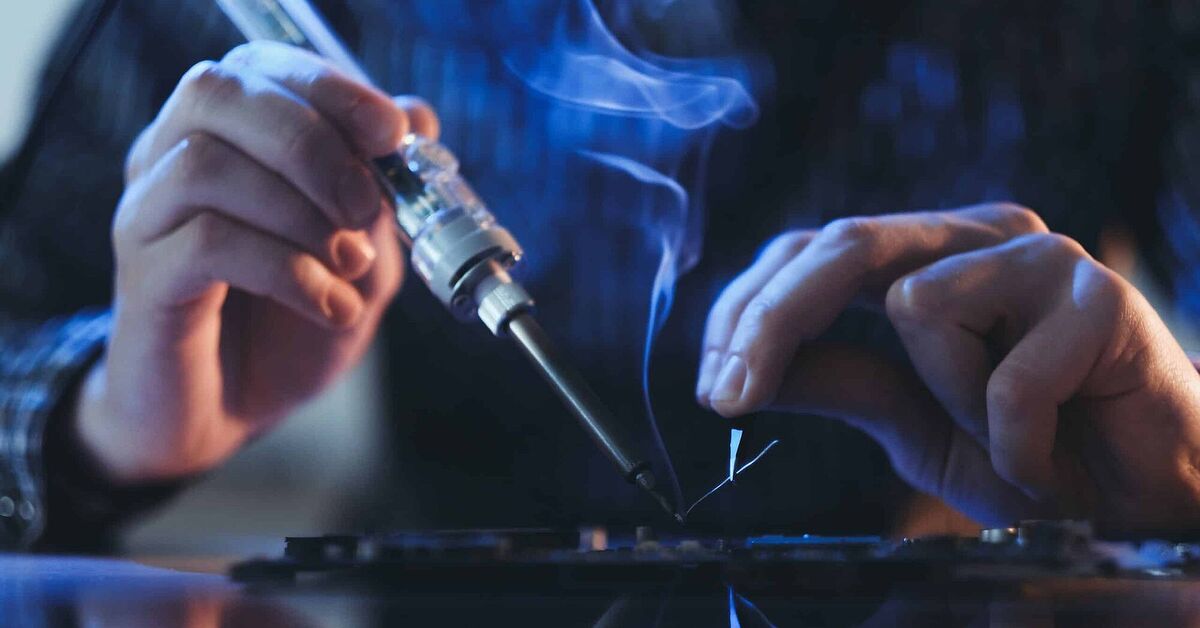